Staying power: Maverick bag-in-box machines powered by Omron Automation platform
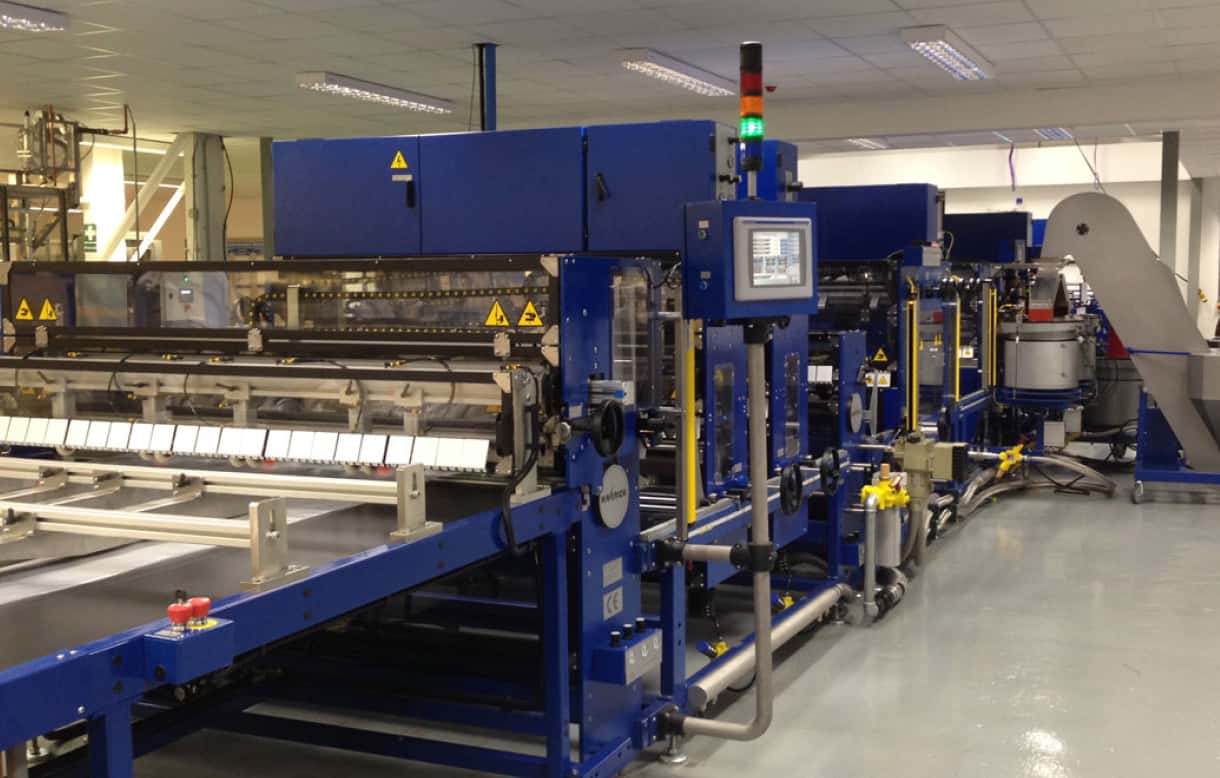
For more than 60 years, Liquibox has built on a legacy of ingenuity to create flexible packaging solutions that set the standard for quality, innovation, sustainability and performance. At Liquibox, you’ll find a commitment to sustainable performance in high-quality solutions that are designed to protect and preserve products all the way to their final destination—whether it’s a wine glass or car engine. You’ll find it in innovative thinking, which leads to breakthrough ideas that solve current needs and future challenges, from better materials to a lower carbon footprint. And you’ll find it in steadfast support as Liquibox works with customers to grow their business.
Machines designed to reduce environmental impact across manufacturing processes
A commitment to sustainable performance flows through everything at Liquibox and is the reason the company chose to collaborate with Omron. Having an Omron automation platform powering the Maverick line of bag-in-box machines for optimal and consistent output means customers can count on Liquibox to deliver the liquid packaging and dispensing solutions needed for today—and tomorrow.
Omron’s control and motion products help Liquibox’s machines deliver 133% higher output.
Not only does Liquibox design and manufacture best-in-class bag making machines for use on all five continents—the company uses them in their own bag manufacturing facilities around the world.
The Maverick line of Liquibox machines champions flexibility capable of handling a range of film types and material sizes, as well as taps and spouts (fitments). This means multiple products can be manufactured in one shift. Quick changeovers and simple-to- navigate machine ergonomics make for less downtime, consistent output and low material waste.
Liquibox’s Engineering Manager, Kyle Brookes, attributes the Maverick line’s optimal machine performance to the Omron automation platform.
“Our machines deliver 133% higher output because of Omron’s control and motion products.” He elaborates, “The machines index faster because the G5 servos work seamlessly with the speed of the EtherCAT network and program scan time of Omron’s automation platform.”
Brookes also addresses the consistency in output, “We produce 100% of our bags within specification using proprietary advanced feed monitoring systems.” These systems are engineered for accuracy using Omron control and motion products as well as sensing components, which ensure the film stays in alignment along the length of the machine within +/-2mm and maintains precise tension control for slitting and cutting.
As for the ease of handling quick changeovers, Brookes attributes that to Omron’s HMI. “Being able to select a variable combination of film types, material sizes and fitments allows our machines to produce a variety of applications during a single shift, with minimal downtime.” Each selection on the HMI triggers a signal that indicates the need to stop producing the current product and to load a new set of raw materials. With the additional guidance of Omron’s motion and control products, the Maverick machines react in near real time, reducing energy consumption and minimizing waste.
Minimizing waste in production: moving toward a near zero-waste future
Liquibox strives to reduce the amount of waste generated during production of all their products. The company works to engineer machines with new technologies to minimize the environmental impact of their manufacturing sites. In fact, their Ashland, OH, USA, plant is 100% landfill free of manufacturing waste.
The films used to produce Liquibox’s bag-in-box products come in high diameter feed rolls. It is imperative for the roll to be loaded on the unwinder properly and then controlled accurately along the length of the machine. This can prevent defects such as wrinkles and slippage—and this part of the process is often one of the main contributors to production waste.
To reduce waste in this capacity, Liquibox relies on Omron’s G5 servos to improve accuracy of the draw, or pulling of the film along the length of the machine so it can be cut at specific intervals to make marketable products. “Liquibox has a tight tolerance of +/-2mm on the draw,” says Brookes. “The servos from Omron allow us to achieve our specification without experiencing over-pull or under-pull.” Brookes can rely on tension remaining constant along the length of the machine, reducing waste from slack or creasing.
“We use films that are more sustainable, that are 20% thinner or that use new resin technologies,” states Brookes. “Working with thinner, stronger and newer films, as well as a variety of different films requires more intuitive temperature control.” Brooks explains that each film may have a different gauge and perhaps a different melting point depending on the material—and both factors dictate the temperature for sealing without burning through the film. “Omron’s E5C series of temperature controllers ensure the temperature on the sealing bars remains stable throughout any production run,” says Brookes. “And they easily adjust to accommodate the temperature variance from any changeover in film.”
Another way Liquibox has been able to minimize waste in production is with sensors. Combined with Omron’s automation platform and G5 servos, the company can ensure proper alignment of film as it travels along the length of the machine. “When used in combination with control and motion products, Omron’s sensors predict and counteract slippage,” states Brookes. Liquibox uses the E2E series of proximity sensors to detect the alignment of film between the guide rails as well as for tracking the accuracy of the draw when multiple layers of film are present for an application. They also use the E3XDA series of fiber optic sensors to detect film position at various critical control points. Both types of sensors provide data to Omron’s automation platform, which then communicates with the G5 servos to adjust speed—making sure the film enters and stays in alignment throughout a production run.
Thinking inside the box: producing lightweight packaging
Liquibox bag-in-box packaging boasts features that are more sustainable compared to industry standard films with improved toughness and durability. Not only has the company reduced the thickness, or gauge, of their films by 20%, they have also reduced the seal length from 15mm down to 6mm—while still maintaining seal strength according to ASTM standards.
The company is able to produce their new, lightweight packaging utilizing existing Omron automation products and processes. “The best practice for handling lightweight packaging is integrating a software platform that communicates between the various automation products and components on the machine. The flexibility of Omron’s software platform allows the entire machine to talk from one process to another,” states Brookes. “Everything works together to compensate for any changes needed to produce the new films, from temperature for sealing, sensing for the different gauges all the way to the motion for speed adjustment.”
In addition to the change in film gauge, the company also handles the reduction in seal length with multiple G5 servos digitally geared for synchronous motion. Liquibox finds them essential to control very precise cutting and sealing in the now smaller area of 6mm.
Liquibox produces 100% of their bags within specification using the Omron Sysmac automation platform.
Creating impenetrable partnerships: building long-term impact
Liquibox maintains a position of creating partnerships with suppliers that have integrity, drive and passion. They also look for partners that offer new technologies with better performance. Brookes notes that one of the biggest factors in selecting Omron as a partner is the support structure. Omron brought Brookes and the Liquibox team of engineers to their proof-of-concept center in Cincinnati, OH, USA, for hands-on experience with the systems and components. “Not only did Omron educate us on best practices for utilizing the entire solution, they were heavily involved with helping us integrate it into our machines and making it work the way we needed it to work to best suit our customers’ needs,” states Brookes.
The company’s main priority is to exceed their customers’ expectations by delivering quality products on time. The engineering team at Liquibox is confident in their ability to do that, thanks to the Omron solution being reliable and consistent, as well as being able to operate within their stringent control parameters. With their machines and flexible packaging products shipping all over the world, they value Omron’s global presence. With a wide array of support services, Brookes and the Liquibox engineering team have access to free technical phone support, local application engineering support and access to local distribution technical experts—anywhere in the world.
“Overall, my experience with Omron is exceptional and has exceeded not only my expectations, but those set forth by Liquibox on behalf of our customers,” states Brookes. “I’m excited to continue partnering with Omron in the future.”
Related pages
Let’s
connect
From greater sustainability to higher performance, we’re here to deliver what your business needs most.